Taiwan’s Largest Steelmaker Faces Green Transition Challenge
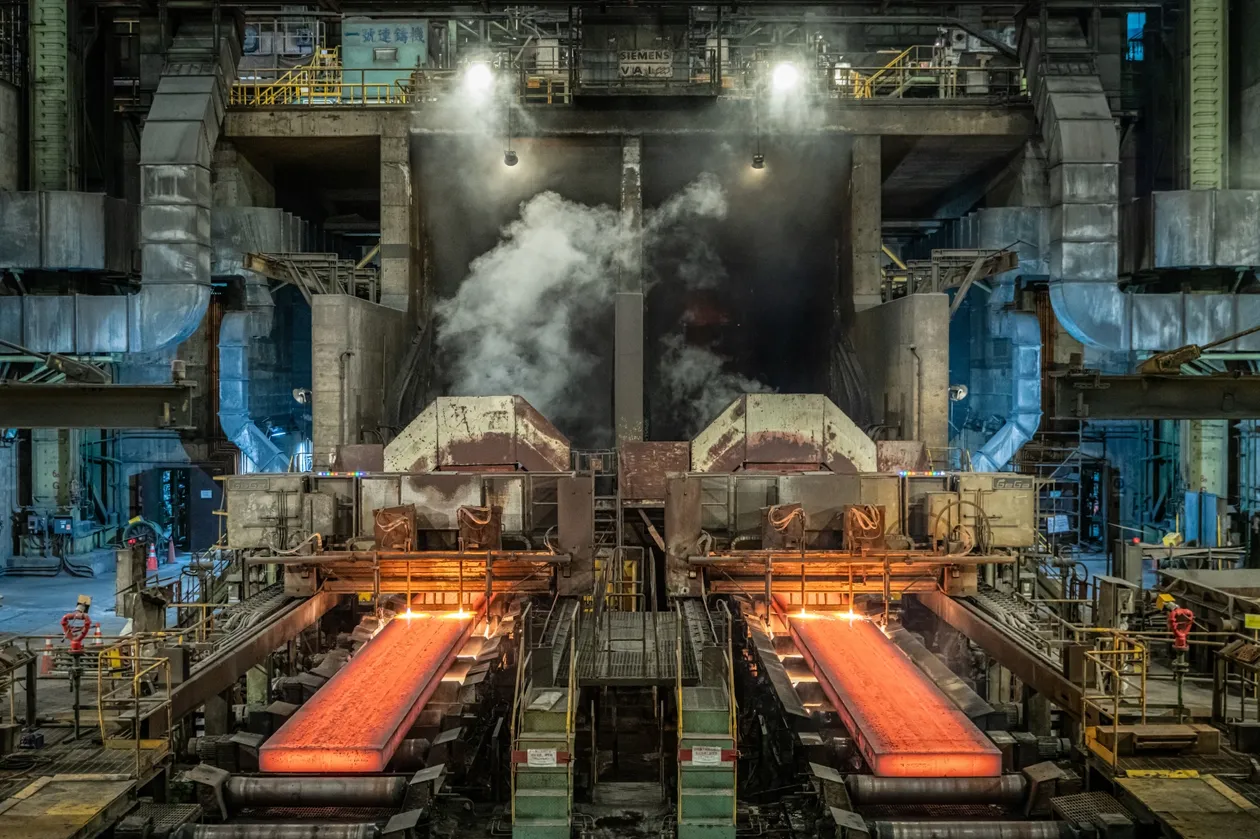
Source:Pei-Yin Hsieh
Taiwan’s leading steelmaker China Steel Corporation (CSC) cannot finance the shift away from conventional coal-based blast furnace production to sustainable steelmaking by itself. While other countries invest huge amounts in the decarbonization of steelmaking, China Steel lacks the financial resources to go green. What can be done?
Views
Taiwan’s Largest Steelmaker Faces Green Transition Challenge
By Kwangyin Liu, Kai-yuan Tengweb only
At 67 Liu Shih-hsien, who has been responsible for developing technical solutions for the decarbonization of steel manufacturing at China Steel Corporation (CSC) for many years, now serves as consultant for hydrogen-fueled steel production.
Liu Shih-hsien. (Photo: Pei-Yin Hsieh)
Today, he has already spent six hours watching over processes at an experimental plant in the southern port city Kaohsiung. Iron ore pellets resembling chocolate chips are placed into a three-meter-high blast furnace simulator. Then hydrogen, used to reduce the iron ore into iron, is slowly introduced into the furnace from the bottom. All eyes are on the reduction process as the technicians try to figure out the speed and temperature for optimal operations. “We are very cautious about feeling our way around,” explains Liu.
As fuels, hydrogen and coal behave very differently. Since hydrogen absorbs heat, it causes the temperature in the furnace to drop. In the worst case this could bring the entire reduction process to a halt, causing severe losses.
“Many technologies are not yet mature, walking toward net-zero is a very risky undertaking,” says CSC President Wang Shyi-chin.
CSC, founded in 1971, mainly produces hot-rolled steel products, cold-rolled steel, steel rods, and wire stock. In 2023 it generated consolidated revenue worth US$12 billion for an after-tax net profit of US$500 million.
The steelmaker’s difficulty to switch to an environment-friendlier production poses a challenge for Taiwan’s entire industry. CSC is not only the company with the highest number of shareholders but also one of the highest emitters of carbon dioxide in the world.
At the Paris climate summit in 2015 a net-zero emissions target by 2050 was agreed among nations around the globe. Therefore, CSC is under pressure to reduce its carbon emissions, and low-carbon requirements have already become green trade barriers.
CSC uses blast furnace and electric arc furnace processes.
Let’s first talk about blast furnaces which have been used in steelmaking worldwide as of now. The raw materials are iron ore pellets and coke, and in the steelmaking process carbon dioxide is emitted as a by-product. When in the future coke is replaced by hydrogen as a reduction agent, the only by-product is water.
Yet it is not as easy as just replacing coal with hydrogen. Hydrogen steelmaking requires shaft furnaces which are completely different from traditional blast furnaces. The shift is comparable to the transition from internal combustion engine cars to electric vehicles, requiring new equipment, new technologies, and a completely new way of thinking.
And then there are electric arc furnaces which use electricity to melt scrap steel. CSC wholly owned subsidiary Dragon Steel Corporation (DSC) in Taichung is CSC’s secret base for low-carbon steel. Just one week before CommonWealth reporters visited the plant, DSC successfully manufactured steel plates containing 60 percent of steel scrap. Even internationally, this is considered quite advanced. The material will be used for chassis for an American computer brand. DSC hopes to raise the share of steel scrap to 90 percent in the future.
DSC’s electric arc furnace process is special as it is also using molten iron from the blast furnace, which allows it to adjust the composition of the steel to a higher quality. Worldwide there are fewer than 10 steelmakers who combine both methods. “They are 20 years ahead of Japan,” said stunned visitors from Tokyo Steel Mfg. Co., Ltd.
(Photo: Pei-Yin Hsieh)
During the transitional period steelmakers around the globe are banking on the “Direct Reduced Iron” process to lower carbon emissions.
The last piece of the puzzle is carbon capture technology which means that no carbon dioxide should be emitted into the atmosphere anymore. Two years ago, a chemical lab was built on the premises of CSC’s Xiaogang plant. It is the largest carbon capture facility in Taiwan.
This pilot plant, which is a joint project between CSC and the Industrial Technology Research Institute (ITRI), captures blast furnace gas and converter gas. It has an annual capacity of 5000 tons of carbon dioxide and carbon monoxide, two greenhouse gases that can be used as raw materials in the petrochemical industry to synthesize methanol, acetic acid and other chemicals, replacing fossil raw materials.
This is an entirely new business model. But even though this carbon capture plant is Taiwan’s largest, it captures only 0.4 percent of CSC’s annual emissions.
CSC's carbon capture facility. (Photo: Pei-Yin Hsieh)
However, CSC is not only facing the challenge of technological change but also lacks capital. Japan and other countries are investing large sums in the green transformation of their steelmaking industries. In contrast CSC has very limited funding to begin with.
On top of that, the steelmaker needs to solve the question where all the hydrogen for green steel is going to come from. After all, hydrogen energy plays a crucial role in the transition.
Taiwan’s hydrogen energy development is in the hands of CPC Corporation, but CPC is currently cash-strapped as well. In April last year, the Executive Yuan launched the Key Strategic Action Plan: Hydrogen which envisions far-reaching goals and division of labor but fails to plan for corresponding funding.
In contrast, Japan has already calculated, based on its latest basic hydrogen strategy, that it will have to spend around US$103 billion in the next 15 years, or more than NT$200 billion per year, to build a hydrogen supply chain. Taiwan earmarked merely US$125 million for hydrogen power in 2023 and 2024 combined, of which US$75 million were allocated to CSC. However, so far, the company has received only US$10 million, whereas CPC has not received any subsidies at all.
Taiwan’s government is offering comparingly little support to the steel industry which renders CSC’s transition to greener production even more difficult.
The German government last year subsidized steelmaker ThyssenKrupp with around 20 billion Euros for the development of hydrogen-based steelmaking. Japan, for its part, invested US$1.5 billion in a Green Innovation Fund which is promoting the green transition of the country’s industry. This includes subsidies to major steel manufacturers such as Nippon Steel, JFE Steel and Kobe Steel to develop the use of hydrogen in steel making in an industry-wide research alliance.
The green transition of CSC does not just concern the development of a single company but pertains to the future of Taiwan’s entire industry.
The Taiwanese government must actively support the green transition of CSC and other companies, providing more financial and technological support, or else Taiwan’s industry will not be able to achieve sustainability goals and prosper in the future.
Have you read?
- Taiwan: Pioneering 'clothing-to-clothing' recycling
- The screw triggering a battle worth NT$200 billion
- Why did Formosa Plastics build its own desalination facility?
Translated by Susanne Ganz
Uploaded by Ian Huang