Minima Technology
Made-in-Taiwan Biodegradable Plastic, Delivering Big for Starbucks and Apple
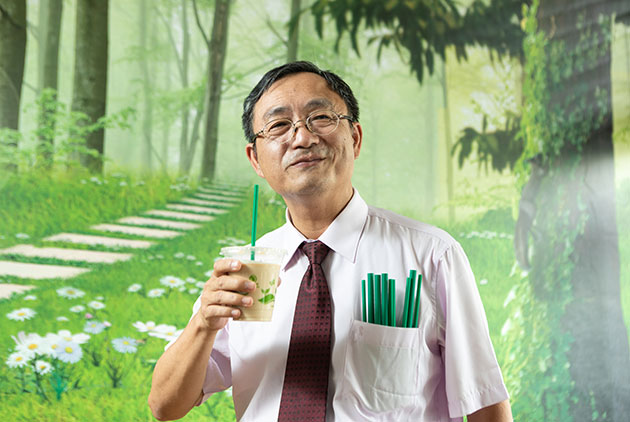
Source:Justin Wu
Taiwan began banning plastic straws in July, but Starbucks in the United States was already shipping in biodegradable plastic straws from Taichung last year. Why have Starbucks, Apple and Formosa Plastics all gravitated to this under-the-radar Taichung supplier?
Views
Made-in-Taiwan Biodegradable Plastic, Delivering Big for Starbucks and Apple
By Kuo-chen Luweb only
When CommonWealth Magazine first meets Minima Technology Chairman Huang Chien-ming at his company’s headquarters in Taichung, he is holding a plastic bag with the image of a green turtle drinking bubble tea and has several green biodegradable plastic straws for Starbucks sticking out of his shirt pocket.
The inconspicuous corrugated steel structure in which he stands conceals the hardships of developing biodegradable plastics in Taiwan over the past 21 years.
That hardship finally bore fruit in April 2018 when Starbucks in the United States contacted the company.
It was just three months before Seattle was about to become the first city in the world to ban non-biodegradable straws. After Starbucks confirmed that Minima’s biodegradable products had received U.S. and international certification, it had the company air freight a large order of the straws from Taichung to Seattle, fully aware that it would be paying mostly to transport air. It had no choice, however, because the biodegradable straws needed to make it to Seattle by the time the ban took effect.
An Eco-friendly Production Model
To meet the demand of 5,000 food and beverage outlets in the Seattle area, including Starbucks, Minima is now using a more environmentally friendly method of production and transportation. It ships 50 metric tons a month of its biodegradable plastic raw material, capable of making 50 million straws, by ocean freight to a straw manufacturer in Seattle that then extrudes the finished product.
And these are just some of Minima’s customers. It also counts Apple and Costco among its clients.
Photo by Justin Wu/CW
So what was it about Minima Technology that drew Starbucks all the way across the Pacific to Taichung?
The story actually began many years earlier when Huang was researching the microbial degradation of plastics for his master’s thesis.
In 1985, Huang was pursuing a master’s degree in chemical engineering at National Cheng Kung University after getting a bachelor’s degree in the same field. For his thesis, he decided on cultivating microorganisms that he believed could consume traditional plastics, hoping to find one he could train for the task to solve the challenge of plastics not decomposing naturally.
To his surprise, he found that no matter how the microorganisms were trained, they ignored Huang’s commands.
“At one point, I thought about reengineering the microorganisms’ genes so that they would be willing to eat plastic. But chemical engineering and biological engineering are worlds apart, and I was forced to give up the idea,” Huang recalls.
Though Huang eventually received his master’s degree, his experiments to cultivate microorganisms to chow down on conventional plastics were a failure.
After Huang later received a Ph.D. in the field from National Cheng Kung University (NCKU), he began his career as a chemical engineering specialist, teaching the subject at NCKU and at Hsiuping University of Science and Technology while also helping others study plastic materials and plastic processing technologies. Because Taiwan was particularly strong in plastic materials and manufacturing, Huang’s services were in high demand and he made a good income.
Struggling in the Business World
In 1998, Huang was made the director of the Plastics Industry Development Center, a nonprofit research organization initiated by the government and plastics industry to help Taiwanese plastics companies develop new technologies and new products. It was a position well-suited to Huang and his strong technical background.
At the time, the world was gradually gaining awareness of the environmental problems created by conventional, non-compostable plastics, and calls to ban plastics were gaining momentum. That triggered efforts around the globe to find substitute materials and plastics that could be broken down naturally. Huang rekindled his master’s degree dream and again searched for ways to break down the stubbornly durable material.
This time, however, he decided against forcing microorganisms to “eat” plastic, instead relying on his years of experience in plastic materials and products to pursue a different path.
“Hundreds of millions of years ago, crude oil was an organism, consisting mainly of a mix of carbon, water and oxygen, all things microorganisms love to eat. So why not look for a plastic from the traditional petrochemical industry that microorganisms actually like to consume,” Huang wondered.
Similar research and methods were sprouting up around the world at the time, including in the areas of biodegradable plastics and biobased plastics. The former are compostable plastics that originate from petrochemicals or from biomaterials, such as grains. The latter are plastics made solely from biomaterials. Polylactic acid (PLA) plastic, which is generally made from fermented corn sugars, is the most common biobased plastic at present.
Photo by Justin Wu/CW
Huang foresaw the future and devoted himself to this arduous approach, but the timing was not yet right. He promoted partnerships between the center and Taiwanese food suppliers and plastic raw material manufacturers to develop biodegradable plastics, but those efforts yielded few results.
To prove the validity of his vision, Huang decided to go out on his own. He set up Minima Technology to continue his research into biodegradable plastics, but he quickly found a general lack of awareness in consumer markets of eco-friendly materials, resulting in low consumer acceptance of and a lack of interest in Minima’s products.
“In the first 10 years of the business, we ran a loss every year and often just burned through money. I would ask friends and relatives to buy the company’s stock, raising NT$5 million here and another NT$10 million there. Whenever we had money, we would press on,” Huang said.
Huang originally owned more than 90 percent of his company’s stock, but he sold so much of it to keep the company afloat that he only owns about 10 percent of Minima’s shares today.
The Turning Point: 2010 Winter Olympics
The company finally made headway in 2010, when the Winter Olympics were held in Vancouver, which had a strong environmental consciousness. The host country declared that it would host an eco-friendly Olympics, and insisted that all of the tableware used at the Games be biodegradable.
But when the biodegradable items it originally ordered arrived in Canada, tests found them to be a combination of starch and conventional plastic. In other words, while the items would partially decompose as the starch was being consumed by microorganisms, there would still be plastic left behind, turning the most environmentally friendly Olympics into a fraud.
Desperate Vancouver officials had to urgently find a substitute supplier, and they settled on Minima, which had international certification and the ability to supply what was needed. Vancouver asked Minima to deliver as soon as possible. Under Olympic rules, only the Games’ official sponsor would normally be allowed to have its brand seen at Olympic venues, but time was so tight, nobody worried if Minima’s products appeared on the Olympic stage with the company’s logo.
This opportunity helped Minima make a name for itself in the international biodegradable materials world. People from around the globe were able to experience Minima technology for themselves, and Canadian media were so intrigued they decided to do stories on the company. The name Minima received a huge amount of buzz, and international buyers suddenly came calling.
At that point, the dark clouds hovering over the company cleared, revealing a bright light, and Minima started to turn a profit. Huang scrambled to rent factory space to satisfy the market’s burgeoning demand.
There was, however, another key factor to Minima’s sudden encounter with success. To promote biodegradable plastics, Huang gave birth to the Environmentally Biodegradable Polymer Association (EBPA), but because none of the top executives at major plastics vendors were willing to become the association’s president, Huang had to take the job himself.
Photo by Justin Wu/CW
International Certification a Big Selling Point
Huang has aggressively pushed for Taiwan to align itself with the international community and pursue certification over the past 10 years, holding international seminars and taking part in the biodegradable associations in other countries. Aside from his role in Taiwan’s domestic association, he is also the chairman of the Pan Pacific Bioplastics Alliance founded jointly with Australia, the United States, Japan, South Korea and Thailand.
Huang’s prominent role in the sector in the Asia-Pacific was a key factor in getting Starbucks to traverse the Pacific to seek out Minima’s help. Not only was “Made in Taiwan” competitive, it was also certified and recognized internationally.
So what kind of straws does Starbuck actually use? Huang explains that research in the chemical engineering field has now proven that microorganisms will consume and break down certain plastics, such as polybutylene succinate (PBS) and polybutylene adipate terephthalate (PBAT).
But being biodegradable is also these materials’ fatal flaw.
“Who wants to buy something that won’t be any good a year from now?” said David Huang, the director of the Ministry of Economic Affairs’ High-Value Petrochemical Industry Promotion Project.
As a result, no major petrochemical vendors were willing to mass produce materials such as PBS and PBAT that nobody was willing to buy. So while these materials have been around for quite a while now, few people were using them, in large part because the way the petrochemical industry has developed over its nearly 200-year history.
Over that time, petrochemical operators, chemical engineering academics and even consumer brands have constantly pursued the ultimate in materials and functions, seeking plastics that are lighter, stronger and more durable. That’s why the world’s big five plastics (PE, PVC, PP, PS, and ABS) are the most used and most sold, with each having attractive properties. Some are extremely versatile, some are soft enough to make plastic bags and plastic wrap, and some are strong enough to serve as automobile fenders, and none of them can be substituted by any other product.
To optimize those plastics to satisfy the demands of industry and people’s daily lives, they have undergone constant R&D, polymerization, and mixing, resulting in materials that microorganisms are less interested in breaking down. It also meant less interest in more eco-friendly materials.
Riding the Global Plastic Reduction Wave
But times and habits do change, and an image of a plastic straw stuck in a sea turtle’s nostril in 2015 suddenly sparked demand for PBS and PBAT after they had been relatively ignored.
That, along with the maturation of PLA technology and the increasing production of that biobased plastic, gave manufacturers different materials to mix and match, and Huang has proven to be a master of maximizing each material’s characteristics.
PLA is a natural biomaterial that does decompose under certain conditions or after a certain amount of time. Today, the transparent iced coffee cup used by Starbucks and the salad bowls used by McDonald’s are made of PLA, but the material does have its drawbacks, even with the advances seen in biodegradable plastics.
Huang said the first generation of these more eco-friendly materials involved adding starch to plastic material. Microorganisms would eat the starch while the plastic would become plastic particles, but the problem was the plastic still existed.
The second generation involved PLA, a material originating from wheat, rice stalks or corn. But the downside of PLA is that it is relatively thick and hard, meaning it takes time and special conditions to decompose, and therefore its applications have been limited.
For many years, however, Huang had been researching the compounding and processing of different materials, which came in handy.
“I’m like a chef, turning different materials into a really good dish. If you only used PLA to make straws, they would be too hard and could hurt consumers’ mouths. But if you add a little PBS, it can soften the product and it is still compostable,” Huang said.
Used His Entire Life to Create Groundbreaking Knowledge
This ability to match materials represented the culmination of this NCKU chemical engineering Ph.D.’s lifelong pursuit of groundbreaking knowledge. But barriers remain to be conquered because so-called biodegradable plastics have yet to be perfected. They do not decompose immediately when dumped in the ocean, and they break down the best when used as compost.
France, Germany and other European countries require single-use plastics to use PBS or other biodegradable materials, but their requirements are tighter. They specify that PBS or PBAT contain 40-50 percent of biomaterials (natural fermented grain) so that they can have a biodegradable plastic without creating too much of a strain on the cultivation and supply of grain.
Have you read?
♦ Turning Ocean Waste into Footwear - Taiwan Makes it Possible
♦ What Makes This Glass Recycling Plant Special?
♦ Serving Clients Like Starbucks and Nike, Arthur Huang Makes Recycling Popular
World Is Watching
A plastic straw stuck in the nostril of a sea turtle has caused the entire world to focus on the problem of plastics not being biodegradable, which has led to massive amounts of plastic garbage clogging the Earth’s waters.
Formosa Plastics’ investment in Minima Technology in June acknowledged this trend. Formosa Plastics Chairman Jason Lin said the company’s sixth naphtha cracker complex is capable of producing PBS and PBAT, and its NT$230 million investment in Minima was an endorsement of Minima’s ability to develop the downstream market for products using those materials.
Combining Formosa Plastics’ ability to create upstream raw materials and Minima’s expertise, the two companies can complement each other in fulfilling their corporate social responsibility and opening up new, profitable commercial opportunities. The partnership also stands to help Taiwan jump on the plastic reduction bandwagon and be in position to take advantage of opportunities when they come.
Minima Technology will be moving from corrugated steel facility in Taichung’s Taiping District to the Huwei section of the Central Taiwan Science Park as early as the end of the year, where it will continue to produce biodegradable plastic materials and products.
Once in its new home, it will become Taiwan’s first tech manufacturer of biodegradable plastic bags and materials located in a science park. But more importantly, it will also have the chance to play an even more important role as the world takes action to rescue its seas and oceans.
Translated by Luke Sabatier
Edited by Sharon Tseng