Servility no longer the way to save Taiwan TSMC: no more night shifts
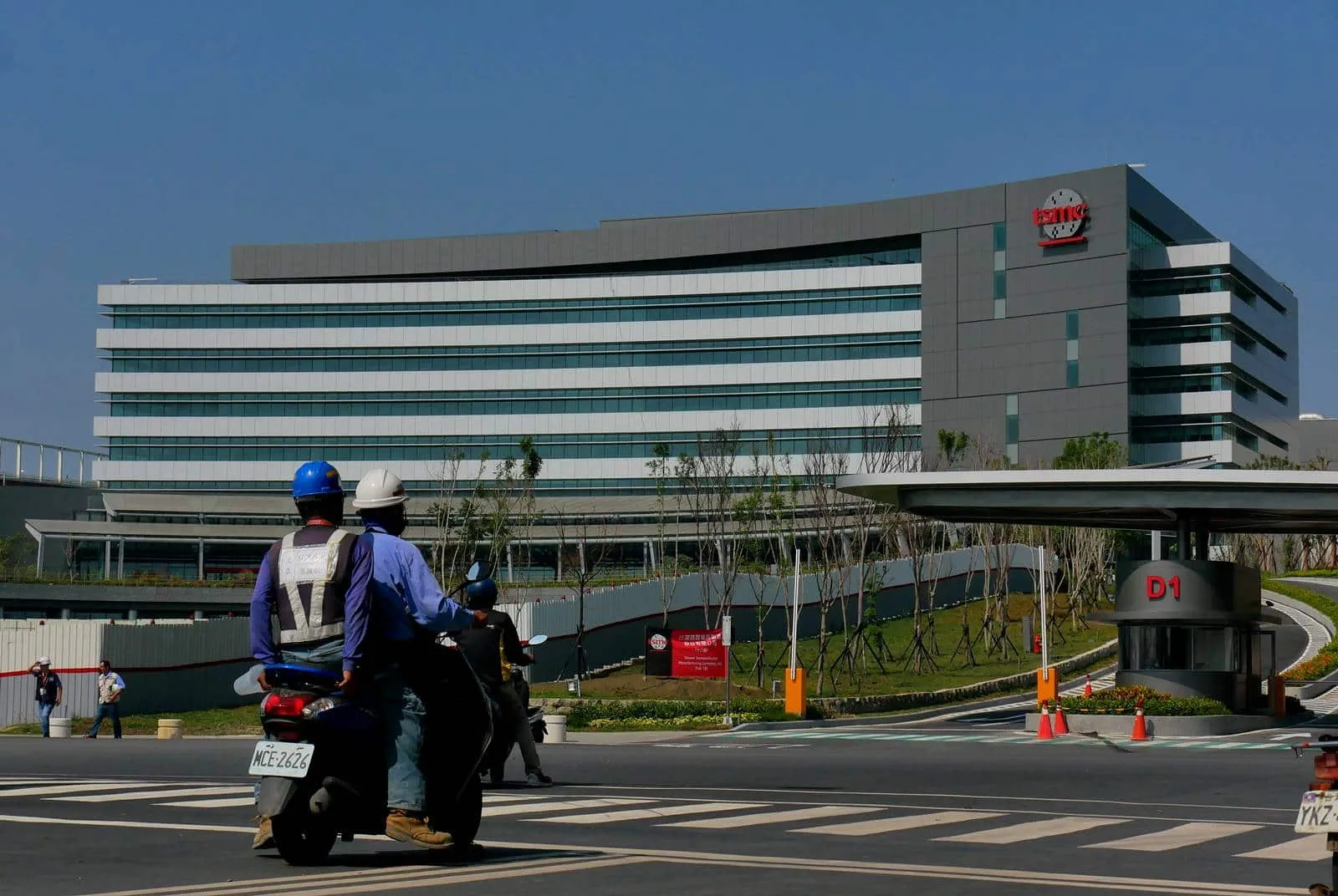
Source:Chien-Tong Wang
TSMC has announced that, about a year from now, equipment engineers will no longer have to do rotations on the night shift. What made them so determined to change?
Views
Servility no longer the way to save Taiwan TSMC: no more night shifts
By Hannah Changweb only
One anonymous equipment engineer at TSMC’s #18 Plant at the Tainan Science Park, a graduate of National Taiwan University (NTU) with six years of work experience at his position, told CommonWealth that his job was essentially “performing work rotations to save Taiwan.” He described working for more than 12 hours a day, staffing the “little night shift” until midnight, and taking on one full night shift rotation every month.
The equipment engineer is the most common, and the most widely-recognized as the most boring and physically taxing job in the semiconductor foundry, or fab.
“Many people can’t take it after one year, quitting very soon! Young people these days don’t have that kind of servile nature,” he remarks. He feels that TSMC is bound to face huge challenges in setting up production in the United States. “The company’s success has relied on wearing out the livers and taking advantage of the servility of Taiwanese youths. But Americans won’t go for that, so we’ll see how they go about finding people (to work) in the U.S.!”
This is truly a cloud cast recently over TSMC, seen as Taiwan’s national economic guardian.
With the company’s technology leading the way, product demand outstripping supply, global expansion underway, and a major recruitment drive ongoing, the company’s deep-rooted manufacturing industry culture is under greater scrutiny from the outside world.
A key statistic, viral online article accelerate change at TSMC
TSMC’s corporate responsibility report indicates that the attrition rate of 2020 new hires reached 15.7 percent, the highest such figure in the past five years.
TSMC stresses that it will prioritize improving this statistic going forward. “Implementing the strategy of putting the right people in the right roles, and lowering the overall attrition rate” are the company’s stated objectives. The key emphasis of future development goes beyond “personnel development” to include “attracting and retaining qualified talent.”
The online article in question, called “Thoughts From an American TSMC Equipment Engineering Undergoing Training in Taiwan”, was shared on Facebook over 2,800 times in early November, and has been the topic of fervent discussion.
In the review of his experience as a TSMC company trainee in Taiwan, the American equipment engineer complained that, although Taiwanese workers routinely work for more than 12 hours per day, they are less efficient than Americans who work daily eight-hour shifts. He noted that they waste most of their time on tasks with no tangible contribution, saying, “I think TSMC might at least approach this in Arizona as it has to compete to retain and attract talent against companies like Intel right across the street.”
During a speech at National Cheng Kung University in November, Y.P. Chin, TSMC senior vice president of operations, admitted that equipment engineers who are forced to work the night shift are the “black hands” of semiconductor fabs.
Consequently, he announced right then that one year from now at the earliest, TSMC equipment engineers will no longer rotate on the night shift. Moreover, they must perform added-value work that consists of more than just “monitoring machines”.
What can TSMC do?
New position: expanded recruitment of Module Associate Engineers (MAE)
The first step is the establishment of a new job position, namely that of Module Associate Engineer (MAE), an assistant to equipment engineers.
In mid-November, Taiwan’s most popular electronic bulletin board, PTT, was flooded with related discussions, much of which centered on the question of whether MAE and equipment engineers would have to take up a share of the work rotation loading.
On its official Facebook account, TSMC directly explained the division of labor between the two roles. “Adjustments will be made to the work shift assignment method and work planning of equipment engineers, from full responsibility for handling the cleaning and maintenance of machines in the past and daily work shifts, adjusted to include feedback for online questions, production line optimization, and the setting of malfunction troubleshooting SOP, to improve the stability of advanced online machines, and cooperation with production line assistant engineers and module associate engineers, so as to continue to lower work shift rotation frequency.”
New skills: accelerate equipment engineers’ AI integration capability, digital transformation.
Chin also played two video clips, explaining the fresh new work content of the “new type of equipment engineer”.
The first clip showed how TSMC first began applying AI to conduct “smart workstation adjustment” five years ago, stressing manual machine adjustments in principle and experience as the foundation, to a success rate of just 60 percent. Now, using extensive historical data, and using AI instead to make automatic adjustments, the success rate has been elevated to 91 percent.
The other video clip showed for the first time how TSMC and ASML used Hololens smart glasses during the pandemic to connect remotely with engineers in the Netherlands, the U.S., and Taiwan, and used MR technology to resolve the issue of the abnormal vacuum degrees of EUVs.
(Adapted from the internet: Hannah Chang)
The two videos subtly convey TSMC’s expectations for equipment engineers and their work and technical abilities going forward.
Chin relates that, in contrast to factory personnel entering the plant to troubleshoot issues, MR remote installation efficiency is slightly inferior. “However, I’m confident that after a few years the differences can be overcome.”
AI-driven automatic machine adjustments stress that equipment engineers should be able to do more than routine workstation maintenance, to include the ability to interpret Big Data, revise parameters, and utilize AI assistance; MR remote installation entails communication with overseas engineers, multinational collaboration, and operating new technology to resolve equipment problems.
Another TSMC employee revealed that quite a few Taiwanese equipment engineers who have volunteered to work in the United States are being trained in using MR. And many engineers are hopeful of being assigned to the Arizona facility three years from now, where they can use Hololens technology to report back to Taiwan and troubleshoot machine malfunctions.
New technology: introducing impressive MR maintenance, VR training with appeal to young people
Promoting impressive VR and MR technology, and announcing to the outside world that equipment engineers’ work has been “elevated” have been part of a full-court image promotion and transformation campaign over the last two months at TSMC, from human resources to manufacturing, to plant operations.
Konrad Young, a former senior research and development department head with 20 years of experience at TSMC, does not believe that TMSC lacks people; rather, it lacks the environment to turn human resources into talent, which explains the high attrition rate. Moving forward, the company will expand the use of new technologies and systematized products to improve processes and forge an efficient work environment.
Fortunately, TSMC already feels the urgency of expectations, has established new work positions, is employing AI, and is using remote machine maintenance technology as the company asks equipment engineers to start undergoing transformations.
Have changes transpired?
The equipment engineer at TSMC’s #18 Plant at the Tainan Science Park reports that he can already feel the effects of the company’s efforts. He says that now his supervisor starts telling him to prepare to get off his shift at 6:30 p.m., and when he is on an all-night rotation, he keeps exhorting everyone to hurry up and hand their work over to the next shift. “We’re all watching to see if it’s just a phase, or if things have really changed,” he adds.
Have you read?
♦ Morris Chang’s master plan for 50 years: The art of sowing despair
♦ Tatung rescue saga drags on with new spate of infighting
Translated by David Toman
Edited by TC Lin
Uploaded by Jane Chen