Why is Asia's 'Tape King' splurging on AI education?
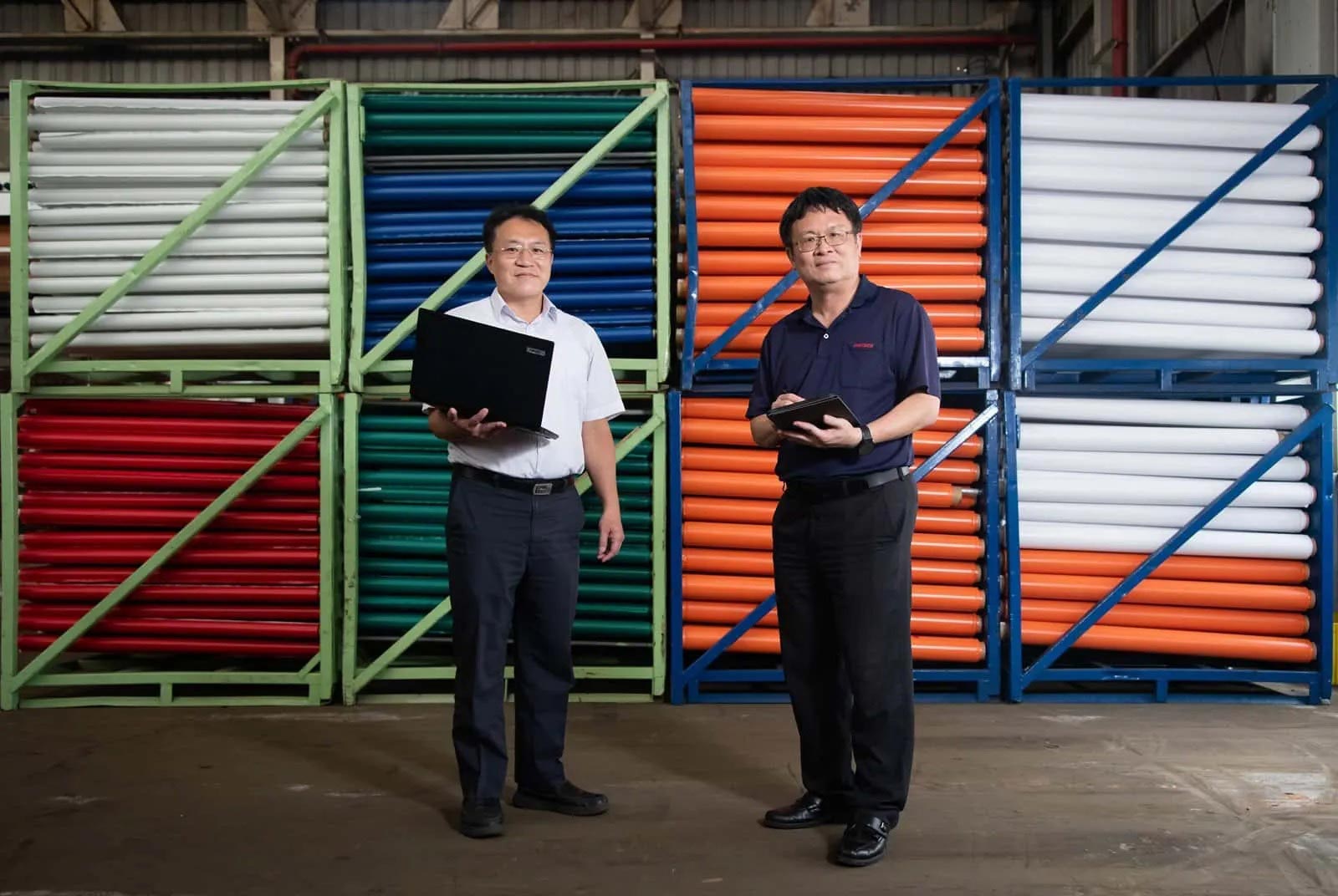
Source:Ming-Tang Huang
Four Pillars Enterprise is Asia’s leading adhesive tape manufacturer. Labor shortages have alerted it to the fact that its hard-earned know-how may be lost as workers age. Its solution? Invest in artificial intelligence.
Views
Why is Asia's 'Tape King' splurging on AI education?
By Ching Fang Wuweb only
Step into the warehouse of Avatack Co. (四維創新材料) in Hsinchu, and you will see adhesive tapes and labels of all colors in varying stages of production. From afar, they look like giant drinking straws. Once the tapes are cut and wrapped, they will be delivered to Taiwanese stores under the familiar Deer Brand (鹿頭牌) logo.
Avatack is part of Four Pillars Enterprise (四維集團), the foremost manufacturer of adhesive tape in the Chinese-speaking world. It has been in the business for 69 years. It makes just about everything that sticks: packaging tape, double-sided tape, electrical insulation tape used for repairs, kinesiology tape for medical purposes, specialized tape for printed circuit board manufacturing, antiviral tape for elevator buttons, beer labels—just about anything you can imagine.
(Source: Ming-Tang Huang)
Four Pillars is a private enterprise. It has factories in Taiwan, China, and Southeast Asia, as well as clients from the world over. With revenue in the tens of billions, it is Asia's largest tape manufacturer.
It may come as a surprise, then, to learn that the tape king of Asia is not only investing in technology for making better tape, but also artificial intelligence.
Automation has come to the old tape factories. I Tsung Chiang (蔣益宗), Vice President at Avatack, shows off an AOI (automated optical inspection) device that is in the midst of conducting a quality check. Human eyes used to be needed to see if the tapes were sticky enough or if there was glue residue. Now, the machine does it all. "The tape is rolling on the conveyor belt at more than 300 meters a minute. No human eye would be able to keep up," says Chiang.
Ever since its founding, Four Pillars has maintained a proud tradition of developing its own production equipment. The AOI device is the result of close cooperation with one of its affiliated companies. In the past, Four Pillars spent an average of NT$100 million dollars a year on investments in hardware in its facilities in Taoyuan and Hsinchu. In an effort to update and automate its manufacturing process, for the last couple of years, the budget has been doubled to NT$200 million.
As for software, the groundwork was laid long ago. There are QR codes on the rolls of paper waiting to be cut and processed. Scanning the codes will reveal helpful information like the serial number, manufacturing date, and more.
Making adhesive tape is not rocket science. There are three straightforward steps: making the glue, spreading it on the tape, and cutting the tape. However, due to the wide variety of its products, Four Pillars has built a comprehensive raw materials inventory management system.
(Source: Ming-Tang Huang)
For example, white is the color of the electrical insulation tape, but what kind of white are we talking about? It can be glossy or matte; the tape may vary in thickness, length, or flammability. And of course, the logos of different clients may be printed on the inside of the tape.
Once you take every factor into consideration, it quickly becomes apparent that the number of possible variants is massive. In the Hsinchu plant alone, the part numbers go up over 100,000. That's dozens of times more than factories in other industries. Not to mention the fact that Avatack sells to the foreign market. "The same packaging tape will not work in both Russia and Africa. You need to adjust the formula for different climates," explains Chiang.
Sending the best and brightest to learn about AI
In recent years, Avatack has gone all out. It has replaced its IT system, migrated to the cloud, and sent employees to attend courses on artificial intelligence. It is digitizing its internal production process.
All of this is because Avatack has spotted a looming threat to its competitive edge: labor shortages.
Some decades ago, Avatack had a memorable marketing slogan: "We have the tape you need". That may still be true, but one thing they are having trouble finding is young workers.
Chun-ju Liao (廖俊儒), CIO at Avatack, says the management has found that an important factor to watch out for during job interviews is the applicant's commuting time, rather than just their resume. Employees who live far away don't tend to stick around. So far, foreign workers and students in cooperative education programs are helping pick up the slack, but the writing is on the wall: Labor shortages are a serious problem that Avatack will have to contend with.
Over the decades, the company has nurtured a band of experts with mastery over the production process of the perfect adhesive tape. They are the secret to its success. But now that the old blood is retiring, it's uncertain what the future holds.
"How to retain talent is what keeps us up at night," says Liao.
The tape-making business is not labor-intensive, but if valuable know-how is not handed down to the next generation, the quality may suffer. The production process has no room for errors. "Ninety-nine percent of the quality is decided the moment you apply the adhesives," says Liao. One misstep can ruin the entire batch. The cost of raw materials is far greater than the labor cost.
In order to retain what the old masters took years to learn, and in order to digitally record all the myriad combinations, Avatack established its IT department half a century ago. Back then, numbers on the machines were hand-recorded and fed into computers to compile a production cycle database. In the last five years, Avatack has hooked up its machines to the Internet of Things so the production equipment can record its own performance.
(Source: Ming-Tang Huang)
In order to put all that big data to good use and really accelerate the smart manufacturing process, Avatack is working with Profet AI (杰倫智能科技), a high-tech startup specializing in enterprise AI software and machine learning platforms for automated manufacturing. Together, they use AI to look for the best way to finetune production.
Profet AI CEO Jerry Huang (黃建豪) says Avatack certainly made an impression. The day they kicked off the AI project, Four Pillars President Yang Hwei-ling (楊慧玲) brought more than 40 senior managers to join the meeting. The next day, Avatack sent over 20 or 30 questions regarding AI, collected from seven different departments. "They were eager to get things rolling."
2% improvement in yield rate
Avatack board member David Lee (李紹唐) observes that President Yang is alarmed at the rate at which Chinese factories are upgrading their capabilities and adapting to smart manufacturing. This sense of crisis has led her to push for the broader adoption of AI solutions. It is an exemplary role model for traditional industries that wish to transform and upgrade their competitive advantages.
Avatack's digital transformation is already bearing fruit. The time it takes to train assembly line workers has decreased by two thirds. Using AI to calculate the best way to make tape also reduces trial and error in the research and development process.
"A 2% increase in yield rate not only saves on material costs, it reduces customer complaints by half," says Chiang. With AI, the root cause of anomalies can be discovered, and abnormalities in the production process can be detected early to prevent waste.
The digital infrastructure built over the last two years may also be used to automate the company's carbon footprint verification process, to be initiated in 2023.
As the saying goes, there's nothing you can't fix with a little tape; the "Tape King" of Asia is hoping that artificial intelligence will do the same for its business. The jury is still out, but the digital transformation of Four Pillars Enterprise is off to a good start.
Have you read
- How did MediaTek’s Airoha become the earbud champion?
- How Amia dominated Taiwan’s PCB chemical market
- Formosa Plastics: Ready to take on carbon?
Translated by
Jack Chou
Edited by TC Lin
Uploaded by Ian Huang