After 25 years, MIT batteries target land, air and sea
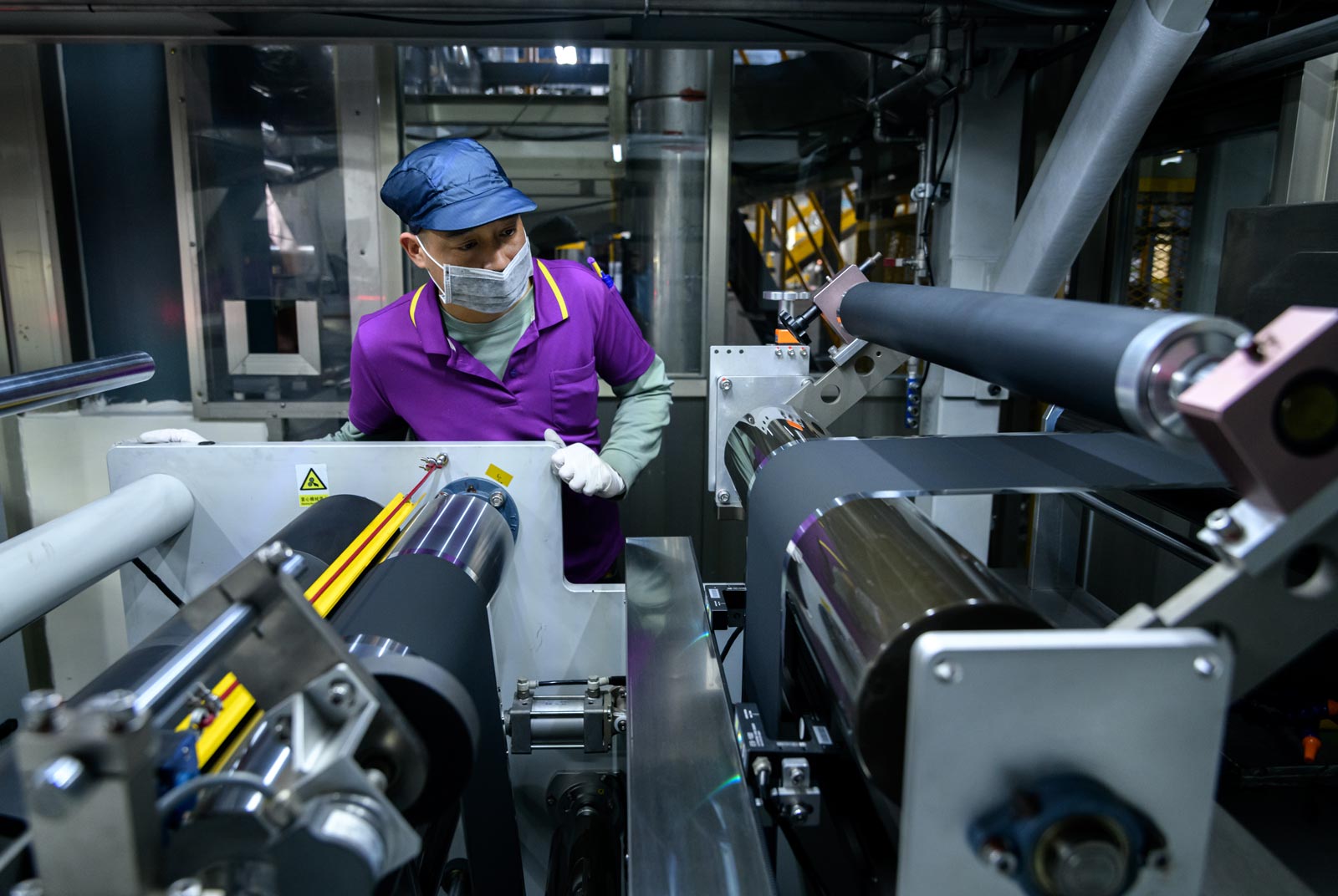
Source:Pei-Yin Hsieh
McKinsey predicts that, due to the rising demand for electric vehicles and energy storage, the global production of lithium-ion batteries will grow at 30 percent annually over the next eight years. This figure will surpass US$400 billion by 2030. Has the time come for Taiwan battery companies?
Views
After 25 years, MIT batteries target land, air and sea
By Chen Kang KangFrom CommonWealth Magazine (vol. 769 )
This enticing business opportunity has attracted many Taiwanese investors. Taiwan Cement, Foxconn, Formosa Plastics, and China Petroleum Corporation (CPC) plan to invest NT$43 billion to produce battery cores, critical materials, and battery modules, making it the largest investment in Taiwan's history.
"Taiwan has a chance in this wave!" says Chen Jin-ming, head of the Materials and Chemical Engineering Institute at the Industrial Technology Research Institute (ITRI).
The battery industry in Taiwan has seen two investment booms in the past 25 years driven by products such as laptops and mobile phones. Yet it has been silenced due to insufficient technical capacities and cost competition.
The Taiwanese battery industry chain can be divided into three major areas: upstream materials, midstream battery manufacturing, and downstream battery modules.
Companies like Advance Lithium (Aleees) and CPC are investing in the research and development of positive and negative electrode materials, which have a high cost ratio and exert a significant impact on battery performance.
Battery manufacturers such as Molicel Energy, Amita Technologies, and Formosa Smart Energy are expected to launch new production capacity within the next two years. Battery modules are Taiwan's strength, and the most famous is the global battery module leader, Simplo Technology, with annual revenue exceeding NT$90 billion.
Why is success possible after 25 years of failure?
In view of the dominance of the top five electric vehicle battery suppliers, China's CATL and BYD, South Korea's LG and SK, and Japan's Panasonic, which account for more than 70 percent of the market share, does Taiwan still have a chance?
Chen believes that, between market expansion and PRC divestment, Taiwan can ride this battery wave.
He offers that in the past, lithium-ion battery usage for mobile phones and laptops did not exceed 100 GWh, but now cars, ships and military equipment have become emerging outlets for batteries, which is projected to reach 3,500 GWh by 2030, growing by dozens of times and forging more space for development.
eVTOL (Electric Vertical Takeoff and Landing) of British company Vertical Aerospace (Source: Molicel)
Secondly, six of the top 10 global electric vehicle battery suppliers are Chinese companies. China's control over the battery market has European and American automakers worried. Trying to find other supply sources, they are working with non-Chinese companies to establish a battery supply chain.
That Taiwan had no major automobile brands in the past could turn out to be a blessing in disguise. Chen believes that since Japan and South Korea have strong automobile brands, battery manufacturers will be more inclined to cooperate with local customers when expanding. However, Taiwanese companies have been forced to go global and ally with overseas customers, giving them better opportunities and the motivation to make inroads into other countries.
“Few countries around the world have a battery industry, and Taiwan has a 25-year industry chain spanning from materials to batteries and modules,” says Chen.
Identifying niche markets and expanding scale through overseas allies that possess resources and end demand is the current strategy of Taiwan's battery industry chain.
Molicel: creating a dream battery for use in NT$90M supercar
Molicel Energy, which has been involved in battery research and development for a quarter century, has always been somewhat of a mystery.
At a recruitment event held at National Taiwan University, Molicel, which is expected to produce 1.8 GWh of capacity this year, unveiled customer product videos for the first time, covering "land, sea, and air" vehicles such as electric ATVs, eFoils, and eVTOLs. The most attention-grabbing product was the Rimac Nevera, the world's fastest electric supercar, worth NT$70 million, which uses ternary lithium batteries produced by Molicel.
“Next year at the Paris Olympics, five eVTOL companies will offer VIP services, four of which use our batteries,” boasts Molicel president Casey Shiue.
Molicel, founded in 1998, began with an eye toward the information products market. After unexpectedly running into cutthroat price competition, it lost money year after year, finally turning a net profit again last year.
How did Molicel break into the high-end battery market? "Through research and development. With continuous R&D, we can anticipate what the market will need in the future, rather than just focusing on the present," says Shiune.
Molicel has constantly felt out its direction of transformation, ultimately coming to the belief that, given Taiwan's limited production capacity, there is no other way but to focus on R&D for small volume, high-priced, high-end products. This is what the company had in mind when, four years ago, it launched the Dream Cell project, aiming to create the perfect battery.
One of Molicel’s clients, the UK-based eVTOL startup Vertical Aerospace, told the media that they had evaluated dozens of battery suppliers around the world, and ultimately chose to partner with Molicel due to the company's ability to deliver batteries with high power and safety features that meet the needs of flying craft. They also noted Molicel’s ability to continuously improve battery performance.
Unlike Taiwan Cement’s efforts to expand its plant facilities (with subsidiary Molicel), Amita Technologies, established 23 years ago, attracted investment from Thailand’s Energy Absolute Group in 2017. The Energy Absolute Group currently holds over 60 percent of shares in Amita.
Amita: Thai multimillionaire in charge - used in boats, trains, and buses
(Source: Pei-Yin Hsieh)
Amita’s Taoyuan battery plant is considered a technology hub. According to company general manager Chris Lee, the company's technical team leveraged their experience with manufacturing and mass production in Taiwan to set up a 1 GWh production line in Thailand last year, with plans to expand to 2 GWh by the end of this year. Amita even has plans in hand for the establishment of a plant with a capacity of 50 GWh.
This rapid expansion can be attributed to Energy Absolute’s existing operations, which span bus, transport ship, and railway companies. The substantial demand for electric vehicles within the group has become a stable outlet for battery exports.
Examples include the 1,250 electric buses that EA deployed in downtown Bangkok last year, and the first electric train that conducted trial operations in January - all powered by batteries produced by Amita’s factory in Thailand.
(Source: Amita)
Chris Lee believes that since batteries must continue to be produced at scale to reduce costs, securing stable outlets is the key to survival for battery manufacturers.
In a petrol-free future, giant elephant turns
The new players in Taiwan's battery industry are the resource-rich petrochemical giants: the Formosa Plastics Group and the China Petroleum Corporation (CPC). In response to the era of non-fossil-fuel transportation, both companies are looking for means of survival after the eventual phase-out of conventional gas-powered vehicles.
The Formosa Plastics Group established a new company, Formosa Smart Energy, with an investment of NT$7 billionB last year, and plans to invest a total of NT$16 billion in two phases to build a 5 GWh battery production line in the Changhua Binhai Industrial Zone, hoping to leverage the group’s resources to make a quick entry into the battery market.
The CPC Corporation, which derives a quarter of its revenue from automotive gasoline, is also feeling the pressure to undergo transformation, taking a two-track approach to forge new ground in the new era using a new business model and critical materials. "Electric vehicles are coming very quickly, and CPC must adapt and make necessary changes," says Lu Kuo-hsu, director of the CPC Green Energy Research Institute.
Seeing the explosive growth in the global NT$400 billion lithium-ion battery market, Taiwanese companies are eager to make their mark on the world stage as soon as this year. Looking ahead, the two biggest risks for Taiwanese battery manufacturers are the stability of large-scale production and control over critical materials.
Large-scale production know-how
GUS Technology, which is expected to produce 1 GWh of capacity starting this April, has shipped products to clients such as Toshiba and Kaneka. Nevertheless, the company is still proceeding cautiously.
(Source: Chien-Ying Chiu)
According to GUS Technology chairman, Dr. Chang Chung-chieh, although customers have recognized the company’s quality in small-batch production, large-scale production at the GWh level remains a challenge. And even though clients have expressed interest in jointly collaborating to establish overseas production facilities, the next steps can only be taken after the verification of shipments from GUS Taiwan’s battery plant.
In particular, to ensure the safety of lithium batteries, car manufacturers require consistent and stable quality. GUS, Molicel Energy, Formosa Smart Energy, Foxconn, and other GWh-level battery production lines will gradually get up to speed, and whether the quality of mass production can gain recognition and catch up with industry peers in China, Japan, and South Korea will be the biggest challenge.
In comparison to the global competition for lithium, Taiwanese companies have barely taken action, and the ability to secure a stable supply of lithium raw materials in the future may be another hidden concern.
“Lithium is very important, due to its scarcity,” relates Formosa Smart Energy president Liu Hui-chi, who recognizes in no uncertain terms that lithium, which accounts for 30 percent of the entire battery, is the key to controlling cost.
The Formosa Plastics Group may be the only Taiwanese company simultaneously searching for mineral sources and refining plants, while investing in recycling technology to ensure a stable supply of lithium raw materials.
If the dominance of China, Japan, and South Korea in the global battery industry is to be broken, the next two years are sure to be critical.
Have you read?
- The scramble for Chile’s lithium: Is Taiwan in?
- Taiwan, Apple making India a new iPhone hub
- From iPhones to Mercedes: How Taiwan’s Kent became top grinder maker
Translated by David Toman
Edited by TC Lin
Uploaded by Ian Huang