Taiwan: Pioneering 'clothing-to-clothing' recycling
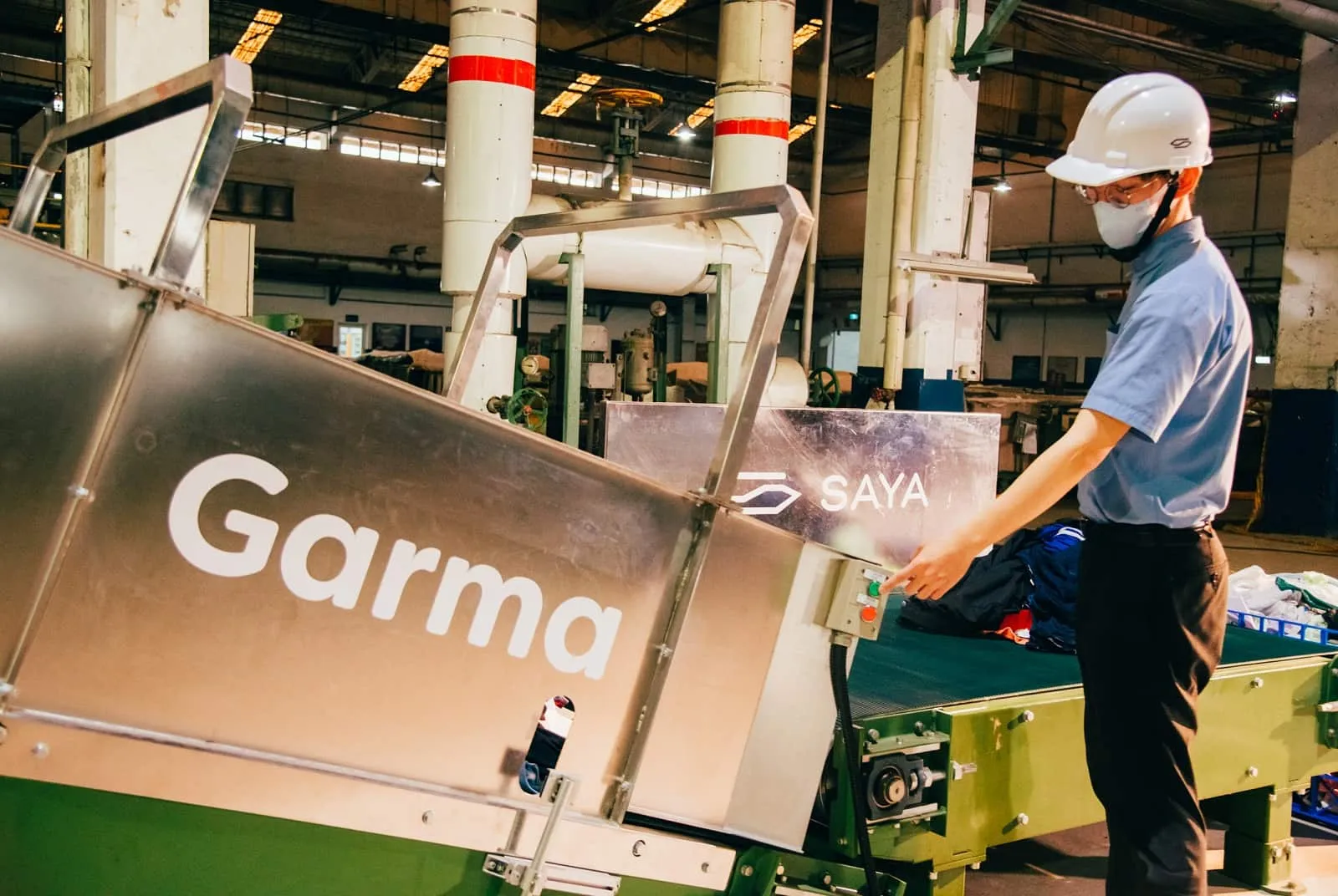
Source:Nan Ya Plastics Corporation
Preparing for the day when yarn from recycled bottles will no longer be seen as eco-friendly enough, Taiwan is poised to become Asia’s biggest producer of clothing made from old clothing next year. However, barriers loom that could slow the process.
Views
Taiwan: Pioneering 'clothing-to-clothing' recycling
By Ching Fang WuFrom CommonWealth Magazine (vol. 787 )
At the end of October, the Textile Exchange held its annual conference in London. Mike Shih (施淙文), a marketing executive with Nan Ya Plastics Corporation’s recycled fibers brand “Saya,” was in attendance and felt that something big was about to happen.
The Textile Exchange is a nonprofit group that brings together the world’s brands, environmental groups, and supply chain members and is responsible for setting and managing several textile standards, including the Global Recycled Standard (GRS).
This third-party standard is observed by brands and supply chains alike; on what constitutes an eco-friendly recycled material, what the GRS says goes.
The beverage sector’s battle for bottles
In recent years, the Textile Exchange has moved toward revising and unifying its many standards, including the GRS, by developing a united standard to better implement strategies that address climate risk.
The Textile Exchange expects to publish this new unified standard in 2024, have it take effect in 2025, and make it mandatory in 2026.
At a round table at the London conference on a draft of the new unified standard, Shih’s premonition came true. A proposal was made that shocked representatives of Taiwan’s textile supply chain – that yarn made from post-consumer recycled bottles should no longer be seen as a viable eco-friendly recycled material.
Polyester accounts for 50 percent of the fibers used in the global clothing industry, and yarn derived from recycled PET (polyethylene terephthalate) bottles has become a critical recycled polyester material for almost every brand. That is especially true for the fast fashion industry, which has accelerated its substitution of virgin fibers with recycled bottle yarn over the past five years to address net-zero emission goals.
Shih observed that while the proposal was currently only in the discussion stage, “it’s just a matter of time before it’s put in place.”
In theory, the main focus of a circular economy should be to turn discarded bottles into new bottles. In the past, however, bottle manufacturers have not treated used bottles as “resources,” allowing textile manufacturers to collect and recycle them into polyester yarn to brandish their environmental credentials.
That meant the material derived from recycled bottles was not being used to make new bottles, leading to voices in the European Union and at the Textile Exchange’s annual conference describing the yarn as “greenwashing” and arguing that it was a “loophole” that needed to be closed.
At the same time, beverage manufacturers in recent years have wanted back into the recycling game, sparking a battle over the collection of used bottles.
Coca-Cola, which produces more than 120 billion bottles a year, announced in 2018 a goal of recycling one bottle for every bottle it produces. It committed to creating a circular “bottle-to-bottle” recycling system using 50 percent recycled materials by 2030, potentially dealing a blow to the textile industry’s access to used PET bottles.
That has put pressure on Taiwan, the world’s third largest producer of polyester, with its textile supply chain potentially being squeezed by both new standards that are increasingly tight and the beverage sector’s renewed interest in bottle recycling.
According to Li Jo-hwa (李若華), head of the Taiwan Textile Research Institute’s (TTRI) Sustainability and Certification section, the European Union (EU) is considering further regulation on the use of recycled materials stemming from fossil fuels.
“They figure that by 2050, there will be a global shortage of fossil fuel-derived material, and new sources of recycled materials need to be urgently developed,” Li said, explaining the EU’s thinking.
Barriers to ‘clothing-to-clothing’ bub
One alternative that has drawn attention in Taiwan’s textile sector is recycled fibers from old clothes, and the country’s chemical fiber giants are ready.
In the coming year, textile giants Far Eastern New Century and Nan Ya Plastics will open experimental production lines to chemically recycle fabric from old clothes, which will yield at least 100 metric tons of raw fiber materials per month. Even that limited production will make Taiwan Asia’s biggest hub for recycling fibers from old clothes.
Before year zero of this “clothing-to-clothing” chemical recycling model, however, there are still three main barriers to overcome.
Barrier No. 1: Carbon emissions attribution
There are two ways to recycle old clothes. One is mechanical, involving cutting up and dissolving the clothes’ fibers before turning them into polyester pellets.
The other is chemical recycling. After the same material is recycled several times, its properties make it harder to treat mechanically. The chemical recycling method relies on chemical additives to break up the molecular structure of the polyester.
Far Eastern New Century Corporation.
Not having to extract more oil by recycling these materials would seemingly be good for the environment, but it will bring large amounts of carbon emissions to the sector.
Because polyester molecules are structurally both huge and stable, breaking them up chemically requires considerable energy and can generate more emissions than producing the virgin material did.
The TTRI’s Li said the textile industry’s most upstream materials are obtained by cracking oil (breaking down complex hydrocarbon molecules), and by recycling those materials, the industry is in essence bypassing the petrochemical sector to produce raw materials on its own.
“It’s tantamount to taking on the original emissions of the petrochemical sector,” Li said, which many in the industry feel is somewhat unfair since users did not have to account for the emissions of those materials when they were first produced.
To see if there are ways to offset some of the burden of these emissions on their environmental standing, Taiwan’s big textile players have commissioned third-party certification organizations to see how the emissions should be calculated and allotted fairly.
Li felt it would be a difficult process because it will require teaming up with the major brands and supply chains in accounting for each node of the process and compiling information from different regions.
If the emissions accounting can be worked out, however, Taiwan could become a model that other regional markets want to emulate because it has the most advanced chemical recycling technology in the world, Li said.
Barrier No. 2: Unstable supply of old clothes
“We’ve estimated that there are only enough old clothes to supply one vendor,” Li said.
Taiwan generates just over 80,000 metric tons of clothes waste per year, of which about 30,000 can be sent to the recycling line. But how much of that can result in usable polyester is a huge question mark, Li said.
One possible direction would be to focus on cutting scraps from clothing factories – the leftover bits of fabric after the patterns are cut from the material – because of the sizable volume available and the consistency of the material. The Taiwanese textile supply chain has many apparel factories in Southeast Asia, with each one potentially generating 1,000 metric tons of waste material a year. Those scraps have typically been incinerated or used to make rags or mats.
At present, however, they are officially categorized as industrial waste, which, by law, cannot be imported into Taiwan.
Li believed that the ability to source materials will be the key to the testing and certification of the big textile factories’ chemical recycling lines in Taiwan, adding that only if the process succeeds in Taiwan can it be exported overseas.
Barrier No. 3: Pricing
If the big global brands want to find new technologies for recycling old clothes, they will either seek out Taiwan’s big vendors or Zhejiang Jiaren New Materials Co., Ltd. in eastern China. That company’s technology comes from Japanese chemical group Teijin Limited, but its capacity is not known.
It is hard to tell if the Chinese company can be considered a competitor.
“We have not yet reached the stage of comparing prices,” said Shih, the Saya marketing executive.
In the current investment phase, the price of recycled fibers from old clothes is so high, “nobody dares ask,” driving customers away. The brands are still watching to see where the new standards will end up and may not make any moves until a year from now, Shih believed.
What is certain, however, is that the R&D for new technologies takes years, and if Taiwanese suppliers wait for the big brands to ask before developing them, it will be too late.
Have you read?
- The world of athletic footwear: ‘Made by Taiwan’
- This Taiwan firm turns PET bottles into Nike shoes and LEGOs
- The ‘hidden champion’ behind Nike and Adidas sneakers
Translated by Luke Sabatier
Uploaded by Ian Huang