Taiwan’s Tesla Boom, and Looking for More
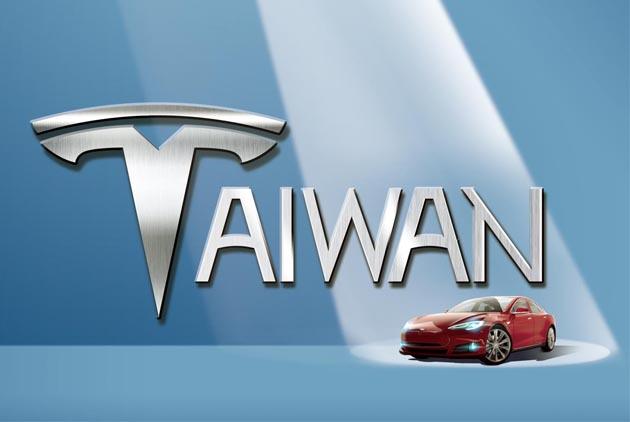
Source:CommonWealth Magazine
Taiwan’s “God of Management” Wang Yung-ching failed at building a car business, but his failure laid the groundwork for the country’s successful Tesla supply chain. What are Taiwan’s advantages in the electric vehicle age and how far can it go?
Views
Taiwan’s Tesla Boom, and Looking for More
By Kuo-chen Luweb only
The global automotive industry is experiencing a paradigm shift, sending Tesla’s stock price soaring and big Taiwanese manufacturers scrambling to expand their production capacity.
At the end of July, Chang Chun Group CEO Suhon Lin (林書鴻) was on the top floor of Chang Chun’s No. 9 copper foil plant, pointing in frustration at a small parcel of unused land in his factory complex in Miaoli County.
“The schedule is too tight; we definitely won’t be able to meet demand,” he said, and then turned to Miaoli Factory General Manager Tsai Chih-chuan (蔡智全), who was standing next to him and wondered, “Let’s see if we can build another factory on that land.”
In 2017, Lin invested NT$27 billion to expand his production capacity in northern Taiwan and overseas, building nine copper foil plants alone in Miaoli County, but just three years later, capacity is still inadequate because of the huge demand for lithium ion batteries for electric vehicles.
No Keeping Up with Orders
Even if Lin does invest more, he would still have trouble meeting his customers’ needs for Chang Chun’s copper foil, which is thinner than a human hair. Lin said that based on estimates of battery demand by international organizations, “building another 60 factories around the world to make copper foil for lithium ion batteries by 2023 would still not be enough.”
The sole supplier of reduction gears to Tesla, Hota Industrial Mfg. Co., Ltd., has also been expanding with abandon. Its first factory is in Chiayi County, a second plant has just gone into production, and a beam-raising ceremony was held for a third factory in May with hopes it can begin production by the end of next year. Company Chairman David Shen (沈國榮) said that aside from Tesla it has completed several projects for European auto makers this year.
So why are factory expansions in the electric vehicle supply chain booming around Taiwan?
The Upside of Wang Yung-ching’s Regret
One key is that the strengths Taiwan developed when it gained footholds in major automakers’ supply chains have complemented Tesla’s weaknesses, and Taiwan’s biggest weaknesses happen to be in areas where Tesla is strong.
“Aside from engines and complete gearboxes, Taiwan can produce all the other components,” Shen said.
This success story actually originated with a seemingly unrelated meeting that occurred nearly two decades ago. Shen recalled suddenly receiving a call one day from Formosa Plastics founder Wang Yung-ching (王永慶), asking Shen to meet with him at Formosa Plastics headquarters.
When they met, Wang, known as the “God of Management,” grabbed a gearbox and asked Shen, “Can you make the exact same thing as this?”
In 1999, Formosa Plastics began manufacturing cars but could not produce engines or gearboxes, and in effect was little more than an assembly plant. Wang knew that without homegrown technology, there would be no future.
“I’m sorry Mr. Chairman, but without the original design drawings or people to teach us how to do it, there’s no way Taiwan can produce engines or gearboxes,” Shen told Wang.
Hota at one point bought two engines and gearboxes and took them apart, reverse engineering more than 500 components. The company made prototypes of all of them to their exact dimensions and specifications, yet still could not put them together.
“Car factories in the West and Japan have been around for more than 100 years and definitely have their own unique experience and tricks of the trade,” Shen said.
In the end, Wang gave up on his automotive dream, but it gave Taiwanese automotive component producers the capability to market their products abroad.
Shen, for example, pushed hard to expand into overseas markets, his gears and transmission shafts gaining footholds in the supply chains of General Motors, Ford, Chrysler and BMW. That’s why when Tesla came calling in 2008, Hota was able to establish itself as the EV maker’s sole reduction gear supplier.
Playing a Mobile Phone-like Game
A second key to the boom in factory growth in Taiwan’s electric vehicle supply chain is that electric car manufacturing has taken a page out of the mobile phone production playbook.
Roger Liang (梁華哲), the chairman of cable assembly and wire harness vendor Bizlink Holding Co., said the supply chains of traditional car makers have had little interest in electric vehicles because their technologies and specs are constantly changing, a major challenge to relatively inflexible Japanese and Western vendors. In contrast, Taiwanese vendors have made their living being highly flexible, investing in opportunities as soon as they see one.
As a result, major international electric vehicle makers are slowly turning to supply chains willing to accept their styles and need for flexibility.
In this world, cars resemble mobile phones with wheels. Driverless and over-the-air technologies relying on the heavy use of data have been critical to Tesla’s disruption of the automotive industry, a massive shift that has played to Taiwan’s strengths.
Bizlink Vice President Younger Wang (王燕超), who is responsible for the company’s automotive customers, cited the example of electric vehicles’ batteries. When you disassemble those batteries, Wang said, you see them as a huge module assembled from 8,000 to 9,000 lithium batteries.
Each of those small batteries uses a wire harness to detect temperature, power, and the discharge rate, generating a massive amount of data every second that is accurately transmitted back to the battery management system.
A Winning IT Foundation
High-speed transmission has been second nature to suppliers in Taiwan because of its strong IT foundation. But century-old Western or Japanese automotive wire harness vendors, who have swatted away all rivals in the traditional car market, may not have the necessary high-speed information technology to compete in this new realm.
Electric vehicles have emerged as the IT sector’s chance to penetrate the traditional car sector, an advantage Tesla automotive light module supplier Excellence Optoelectronics has used to emerge victorious.
Excellence President Fanny Huang (黃昉鈺) said Tesla is particularly focused on LED car lights saving power, a demand that has helped her company overcome conventional automotive car light suppliers.
“Their (traditional suppliers’) strengths are production tools, lamp housings and plastic and metal parts, but they don’t have the expertise of power-saving technology,” she said.
Excellence can help customers with the design of their products, including how to maximize their reliability, energy efficiency and cost-effectiveness, Huang said.
Still, breaking into the Tesla supply chain can be difficult. So why was Tesla willing to take a risk on a relatively small Taiwanese outfit rather than a big LED maker, such as South Korean giant LG?
The reason touches on the third key to the factory boom – the flexibility and capacity for innovation of Taiwanese suppliers, which have enabled them not only to win but to far outpace their rivals.
“If we were only 5 percent cheaper, they wouldn’t have given us an opportunity,” Huang recalled. “So we demanded of ourselves that we lower our costs by 20 percent, improve our reliability by 20 percent, and reach 20 percent power savings, and be able to help clients solve problems and do design work together.”
Hsieh Lu-lin (謝騄璘), a senior analyst with the Industrial Technology Research Institute’s Industrial Economics and Knowledge Center, said Tesla has used non-traditional thinking to build cars and lead its supply chain. It encourages vendors to work with Tesla in researching car systems to see where they can be improved and refining those ideas to foster truly disruptive innovation.
Taiwan must seize on that if it hopes to continue to prosper, Hsieh said. In the past, Taiwanese manufacturers would receive orders and produce them, but they now have to go a step further, helping clients score breakthroughs, such as how to use fewer resources while building more cars.
Plotting the Circular Economy
Enter Chang Chun’s No. 9 copper foil plant in Miaoli and one notices that its raw material comes from copper extracted from waste electric wire and cable. After the material is turned into a copper electrolyte, a charge of 50,000 amperes is sent through it to draw a 5-micron thin foil. It took Chang Chun eight years to gain the experience and technologies needed to perfect a technology most of its competitors have yet to master.
The only other company in the world that can meet this standard is Japan-based Nippon Denkai.
Another key material used in batteries is cobalt, produced mostly in the Democratic Republic of the Congo. Only 100,000 metric tons of the rare metal are produced globally a year. But while controversy brewed over cobalt mining practices, Taoyuan-based Mechema Chemicals International began researching how to recover cobalt from petrochemical catalysts to reduce dependence on mining.
Yet, even as Tesla’s stock price soars and sales of electric vehicles surge, Mechema Chairman Yen Lung-tsai (嚴隆財) seems in no rush to expand capacity, focusing instead on his next move.
Lithium ion batteries currently being used in electric cars are expected to degrade by 2025 and start to be replaced, Yen said, which is why Mechema is developing technologies to recover cobalt and nickel from used batteries and recycle those materials back into the battery supply chain.
Future Challenge: Going beyond Contracting
Tesla demands that its suppliers be both flexible and agile, and just as getting a foot in the Tesla door can be difficult, getting booted is equally unusual.
Quality and safety are the main tenets of any car manufacturer, and Tesla is no exception. Certifying suppliers can take three to five years, which is why Taiwanese companies, which account for 75 percent of Tesla’s supply chain in terms of numbers, are hard to replace.
In the future, however, Taiwanese factories may have to consider setting up shop in China because Tesla is demanding that the percentage of locally sourced parts for its Chinese-made cars be increased. For the Model 3, the goal for local content is 80 percent by the end of this year, up from 30 percent when the car was first produced there. Currently, Tesla’s production in China accounts for 20 percent of its worldwide output.
Alternatively, Taiwanese vendors could decide to develop markets outside of China.
“Taiwan has competitive advantages in markets outside of China. The opportunity at the very least is 750,000 Tesla vehicles,” Hota’s Shen said.
A key part of the third plant Hota is building in Chiayi is an R&D center featuring seven divisions, with the materials, production processes, and defect strategy divisions all focused on quality issues.
Shen feels Taiwan should not be satisfied simply with supplying Tesla, and instead have the courage to pursue an electric car dream.
Bizlink’s Liang agreed.
“Because Taiwan’s electric car supply chain took off at about the same point as those in Europe and Japan, it has an opportunity to overtake them,” Liang said. “Taiwan’s signal transmission technology and electric motors have competitive advantages, and it could start with special vehicles and vehicles used to move cargo. At the very least, they could first meet domestic demand.”
Taiwan in fact is capable of manufacturing complete lithium ion batteries, as home appliance brand Dyson has shown by sourcing its lithium batteries in Taiwan.
Chang Chun’s Lin cited the possibilities within his own company’s areas of specialization – chemicals and materials. Taiwan is capable of developing the cathode materials, anode materials, isolation film and electrolytes lithium ion batteries need, but could use some help from the government in backing a domestic battery industry, Lin said.
“The government should strengthen its support for the industry. Sales of electric scooters are growing faster in Taiwan that anywhere else in the world, and this is an opportunity that cannot be missed,” Lin said.
If Taiwan does not move in that direction, Lin warned, its single-minded focus on contracting will lead to a repeat of Wang Yung-ching’s fate of not having his own brand or technology and ultimately deciding to shut down the business.
Taiwan’s OEM assemblers often serve as little more than punching bags for international brands searching for the best prices. From shoes and apparel to desktops, laptops and mobile phones, Taiwan has never been able to escape this fate.
But with electric cars creating a paradigm shift in the industry, it may be the wrong time for Taiwan to get complacent and settle for manufacturing parts for Tesla.
Instead, now is precisely the time to search for ways to reverse its destiny of playing second-fiddle to the big vehicle brands.
Have you read?
♦ Burned by Huawei Ban, Qualcomm Document Implicates MediaTek
♦ Gogoro’s EV Dream Facing Major Headwinds
♦ Retaliatory Consumption is Here! As Lockdowns Ease, This MIT Product is Spinning Away
Translated by Luke Sabatier
Edited by TC Lin
Uploaded by Penny Chiang