Chang Chun turns CO2 into chemicals
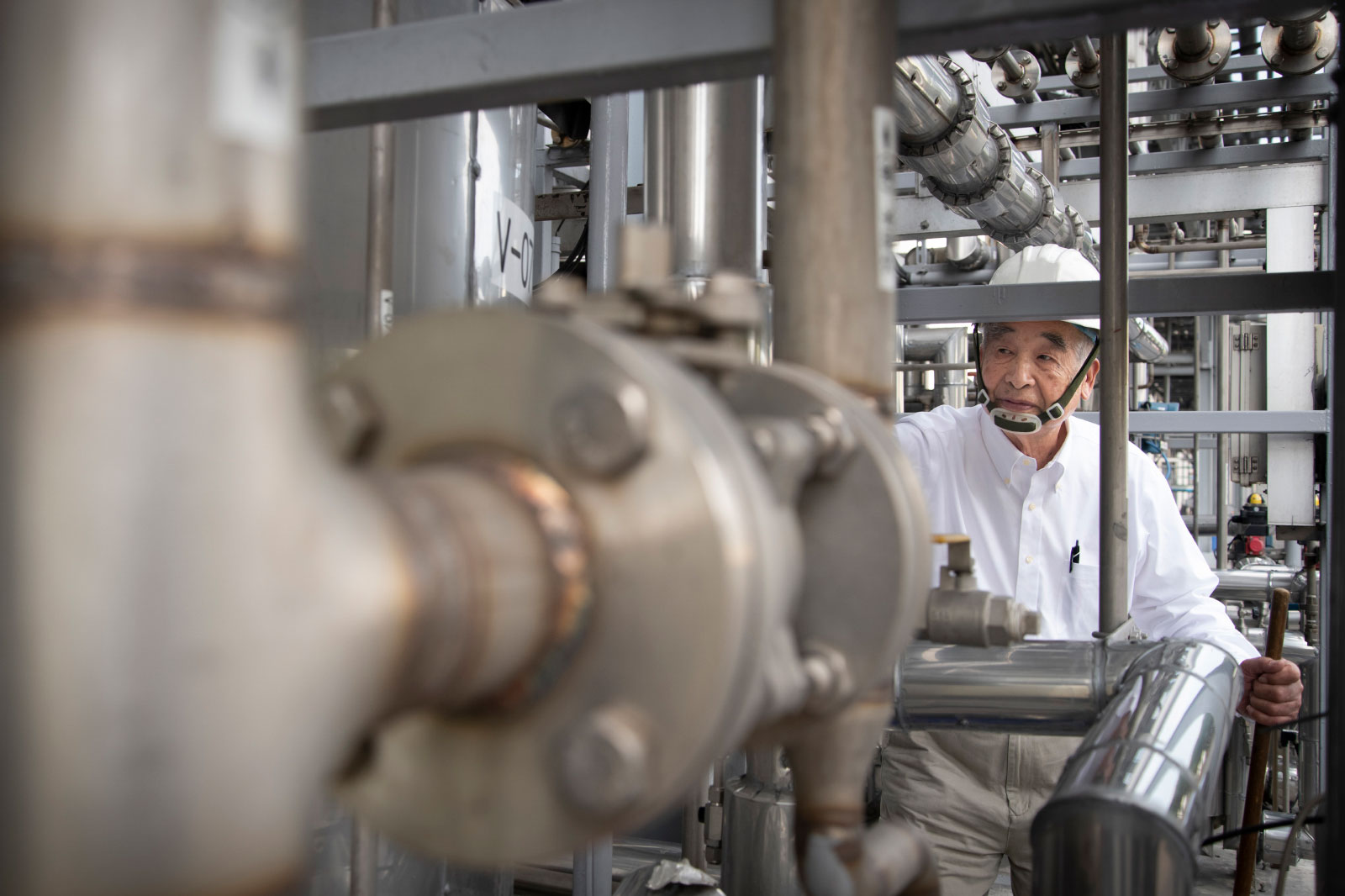
Source:Ming-Tang Huang
British Petroleum once sued Taiwan’s Chang Chun Group for producing a valuable chemical compound. Today, Chang Chun reuses the carbon emissions from its production to synthesize acetic acid. Once derided as a money-losing business, it is now one more reason why Chang Chun is unique in all the world.
Views
Chang Chun turns CO2 into chemicals
By Kwangyin LiuFrom CommonWealth Magazine (vol. 744 )
Suhon Lin, Founder of the Chang Chun Group, is 94 years old. He is a living historical figure from Taiwan’s petrochemical industry. In the 70-plus years he has devoted to petrochemicals, he has been honored as Taiwan’s “Petrochemical Edison”. Even when he takes a swim, he is thinking about how to refine the production process.
In 1949, 21-year-old Lin and his partners Liao Ming-kun and Tseng Shin-yi founded Taiwan’s first plastics factory in Taipei: Chang Chun Plastics Co. Their first hero product was glue produced from urea. Used to manufacture plywood, it was the company’s first major export.
Founded on a book and a chemical formula
Lin takes out a Japanese book titled “Organic Chemical Manufacturing Industry” with great care. He finds a chemical formula within; it is the recipe for producing glue.
(Source: Pei-Yin Hsieh)
Chang Chun was founded on this formula. Once an unremarkable little factory, it has now grown to be a conglomerate that makes NT$400 billion in annual revenues and has operations across ten countries.
Chang Chun’s Dafa Factory in Kaohsiung has nearly five decades of history. It is the home to many Taiwan firsts, and even some world firsts.
The engineering plastics used in automobiles and electronics are manufactured from two compounds known as 1,4-Butanediol and allyl alcohol. The Dafa Factory leads the world in the production of these two elements; it is also the second-largest manufacturer of acetic acid, also known as ethanoic acid or vinegar acid.
What’s even more impressive is the fact that Chang Chun has taken carbon emissions, which every company wants to get rid of, and turned them into a source of wealth. It is recycling the carbon that is a by-product of its manufacturing process and using it as an ingredient in acetic acid.
Take a walk around the Dafa Factory, and you will see petrochemical pipelines of every color. You may also see Lin touring the plant, followed by an entourage of assistants furiously taking notes.
Every Chang Chun plant in the world has a long wooden cane lying about for just this purpose.
Lin walks like the wind. He needs a cane not because he has become unsteady on his feet, but because he likes to point out problems with his cane. He even sometimes sticks the cane into a factory’s gutters to see if the discharge smells odd.
(Source: Ming-Tang Huang)
Lin is pleased to speak about Chang Chun’s role as a pioneer in the business of recycling carbon. "We have been thinking about using carbon dioxide to make acetic acid for twenty years,” he says.
Chang Chun needs acetic acid to produce both polyvinyl alcohol and vinyl acetate. Its plant in Taiwan needs 500,000 metric tons a year, and the plant in Singapore needs 200,000 tons a year. In the past, they had to import from the U.S.; but Lin saw no reason why it could not be manufactured domestically.
Research and development take up 10% of Chang Chun’s annual revenue. More than a decade ago, Chang Chun designed its manufacturing process and subcontracted an American factory to help build the equipment. This subcontractor also made acetic acid production equipment for British Petroleum (BP).
In good faith, the American subcontractor gave Chang Chun advice on how to improve their tools. But after getting the delivery, Chang Chun also received a letter from BP’s lawyers: they were suing Chang Chun for infringing on their patent.
“You had to hand it to BP,” says Lin. The two conglomerates settled out of court. “Their demand was that we had to buy acetic acid from them.”
Chang Chun had no choice but to sign a purchase deal for five years. But Lin was not going to take this sitting down. He knew he had to find a way around the patents if he was going to produce his own acetic acid.
Going for broke to produce acetic acid
Finally, through a German contact, Lin came to be in touch with the American company Eastman Chemical. They were willing to license the technology of producing acetic acid to Chang Chun.
“I could not let it go, I wanted to see it through,” says Lin.
It was not enough just to make acetic acid. Lin has a flair for research and development. He saw that the conventional method of producing acetic acid emitted a great deal of carbon, because you had to produce carbon monoxide with coke, and then trigger a chemical reaction by combining it with methanol.
Lin had a flash of inspiration. The process of churning out chemical products naturally created a lot of carbon dioxide. If the carbon dioxide could be converted to carbon monoxide, then the waste could be transformed into fuel, and emissions could be reduced along with the costs.
“Even back then, academic experts warned us that petrochemical companies, oil refineries, steel plants—all these major carbon emitters would one day have to face the music,” says Lin. That is why as far back as over two decades ago, he thought about changing the way Chang Chun produced acetic acid.
Today, Chang Chun has the world’s only commercialized production process for recycling carbon emissions to manufacture acetic acid. Chang Chun’s plant in Mailiao collects over 84,000 tons of carbon dioxide every year to produce acetic acid. The annual yield of acetic acid is 750,000 tons. Chang Chun has finally fulfilled its dream of producing its own acetic acid instead of importing it.
Chang Chun is a global trailblazer in converting carbon dioxide to acetic acid. At first, many within the company were against the experiment.
“I was also one of those who was against the idea,” CEO Su Shih-kuang says sheepishly.
The main sticking point was that at the time, it didn’t offer enough commercial value. Su adds that the minimal internal rate of return of Chang Chun’s products was 12%. But the acetic acid production process lost money for many years.
After more than a decade of investments, the venture has finally borne fruit. The process of converting carbon dioxide to acetic acid will have commercial value now that carbon credits can be traded.
(Source: Pei-Yin Hsieh)
Even Su is unable to explain how Lin foresaw the future more than twenty years ago. “All I can say is, he is a man with a vision,” he says.
Chang Chun also works with universities to develop groundbreaking technologies. By working with National Tsing Hua University, Chang Chun built an experimental carbon capture plant at the Dafa Factory’s cogeneration facility in 2019. They tried various kinds of catalysts to discover the best combination.
Committing one-third of all R&D personnel
Even though they can only capture 100 kilograms of carbon dioxide per day at the moment, Chang Chun’s long-term plan is to use the captured carbon to develop new chemical products.
In the past six years, Chang Chun invested nearly NT$200 million in funds, and committed more than 70 R&D personnel who have MDs or PhDs—a third of the entire R&D staff—to work with Honorary Professor Chung-sung Tan of the Department of Chemical Engineering at National Tsing Hua University.
In any case, the experimental carbon capture plant is just the beginning. “In the next ten years, the biggest challenge that Taiwan’s petrochemical industry will face will be the matter of carbon emissions,” says Lin in all seriousness.
(Source: Ming-Tang Huang)
Even though the top-three importers of Taiwan’s petrochemical products—China, the United States, and Vietnam—are currently on the fence about following the European Union’s example of imposing a carbon tax, it is indisputable that carbon credits are the future. “In the future, if we account for all the taxes, Taiwan’s petrochemical exports may lose their competitive edge,” says Lin.
He predicts that the international carbon tax rate will be at least US$30 per ton of carbon emissions. Whether a foreign government or the Taiwanese government collects this tax is irrelevant. Petrochemical prices will go up, there is no doubt about it.
A long way yet to go
Lin never finished middle school himself. But he is leading a team of over 200 researchers with MDs and PhDs. Chang Chun has always committed a tenth of its staff to research and innovation. The company holds over a thousand pages of patents.
Where did this passion for research and development come from? “There is nothing that cannot be made better with better technology,” Lin says. Because of this unwavering spirit, Lin has a finger in every pie, from chemical products used in the semiconductor industry, to electric vehicles, to 5G and even the metaverse.
In the past, the petrochemical industry defined the nature of human civilization. The future of the petrochemical industry will be to find solutions to many of mankind’s problems.
For Chang Chun, the first seventy years of its existence was just the beginning. There is still a long way yet to go.
Have you read?
♦ The Edison of Petrochemicals
♦ TSMC’s bold net zero pledge: Cutting a Taipei’s worth of emissions
Translated by Jack Chou
Edited by TC Lin
Uploaded by Penny Chiang