How do BASF and Covestro make their greenest petrochemical products in Taiwan?
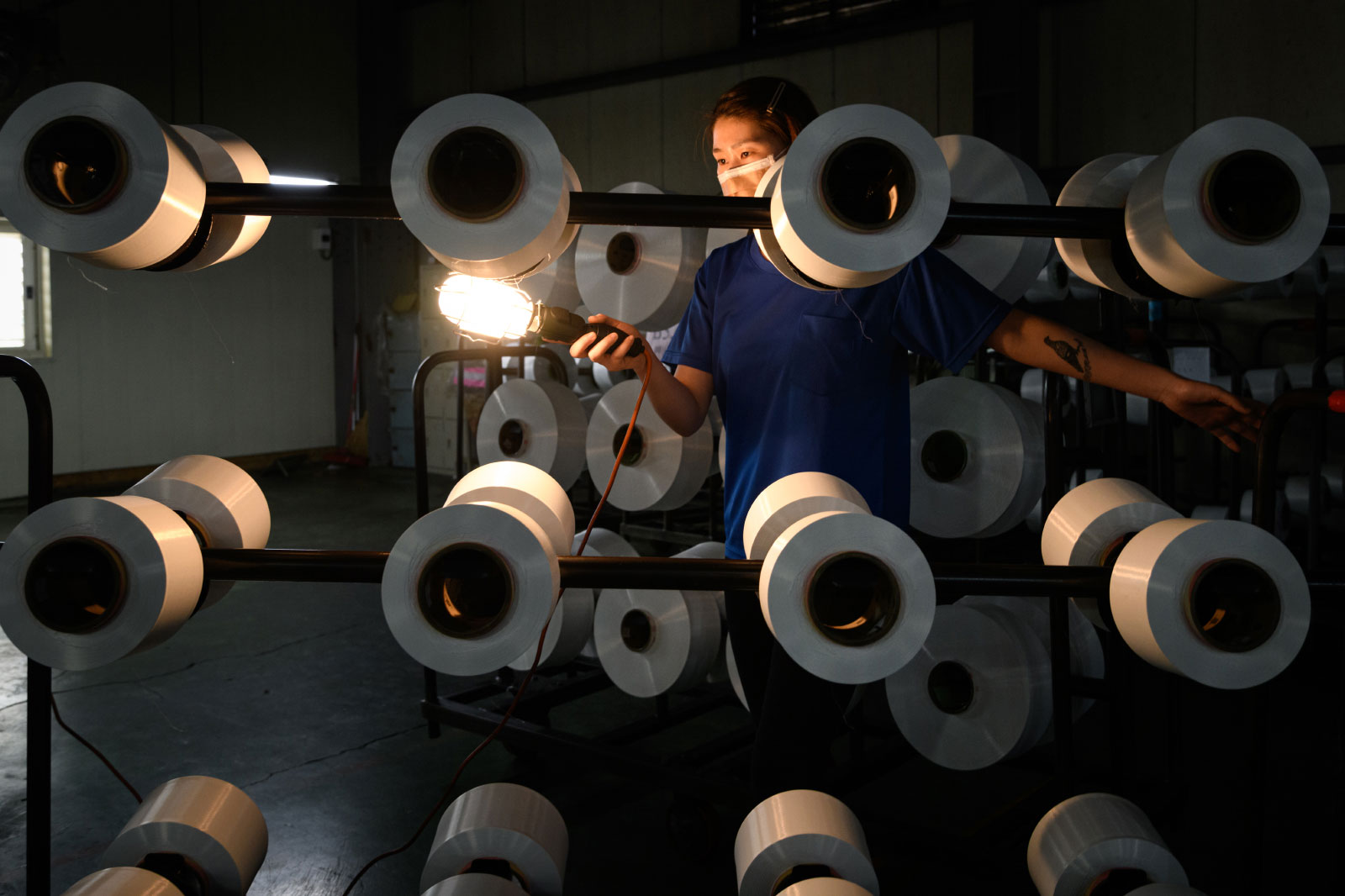
Source:Pei-Yin Hsieh
Today, low carbon and recycling have become mainstream global trends. Major German industrial conglomerates such as BASF and Covestro firmly believe that sustainability is key, and Taiwan is playing a critical role.
Views
How do BASF and Covestro make their greenest petrochemical products in Taiwan?
By Ching Fang WuFrom CommonWealth Magazine (vol. 744 )
Europe’s “greenest” petrochemical products have found their way to Changhua in central Taiwan in recent years, and are now making their way to the global market.
A thin white nylon thread is formed on a machine in Italon Fiber’s plant, situated in Ershui, at the southern end of Changhua. This batch of nylon yarn spent its past life not as petroleum, but discarded tires.
After being broken down by thermal cracking, tires are formed into nylon slabs. Next, they are sent to Taiwan for thread extraction, and finally to be made into functional clothing for an outdoor sporting brand. Over the course of this process, the CO2 output is just half of that of producing the raw material.
This is the result of the German BASF corporation’s investment of NT$500 million two years ago in its ChemCycling program.
(Source: Pei-Yin Hsieh)
“Before, there wasn’t much recycled nylon yarn; most of the raw material was recycled factory scraps,” observes Hsu Hsiao-ming, deputy director of Italon Fiber.
Now, customers are keenly interested in nylon thread from recycled materials, with some even claiming a recycling rate of 100 percent.
Crossing Changhua over to the northern county line to Xianxi Township, the German company Covestro, one of the world’s three largest manufacturers of TPU, operates its biggest Asia-Pacific manufacturing base. TPU offers flexibility between that of plastic and rubber, and is suited to a wide variety of applications including sofas, water-resistant jackets, running shoe soles, and mobile phone cases.
Last September, Fairphone, the world’s first mobile phone brand to promote sustainability as its key appeal, introduced its latest-generation handset. The case, the first of its kind made with 100-percent recycled materials, was manufactured by Covestro from recycled scraps to produce shock- and impact-resistant phone cases.
The rear cover, middle frame, and wireless charger are made from recycled polycarbonate (PC) produced by Covestro. In its “former life” before being repurposed, it was 19-liter industrial water jugs from Farmer’s Spring, China’s biggest manufacturer of packaged drinking water.
A full 60 percent of the Fairphone 4 is made using recycled materials, the highest proportion among all smartphone brands. Starting in 2019, the R&D team searched far and wide among over a dozen companies to source recycled materials. And after enquiring with nearly every petrochemical enterprise in Taiwan, only Covestro responded positively.
As brands give play to recycling and sustainability, Fairphone senior mechanics engineering manager Oscar Chang observes that very few mid-stream injection-molding vendors have experience in the contract manufacturing of sustainable materials, and it is now a hot item.
BASF: Once-in-a-century transformation
When it comes to an international model of sustainability in Taiwan’s petrochemical industry, the venerable name of BASF, with 150 years of history, is sure to come to mind.
The BASF Group’s annual CO2 emissions currently stand at 20 million tons. By 2030, the company expects to invest four billion euros to cut emissions in half, and to ultimately achieve carbon neutrality by 2050.
To accomplish this, BASF must first radically transform the conventional crackers used to produce raw chemical materials, completely changing over from burning natural gas and other petrochemical fuels to green energy. If it is successful in developing these methods, it will be the first electrically heated cracker in the industry. Starting in 2035, the corporation’s demand for electrical power is estimated to be over three times the present level.
With this in mind, BASF is working on plans to double down on renewable electricity as well as investing in wind farms to secure sources.
“We’re the first chemical company to include CO2 reduction among our KPIs” (key performance indicators), notes Kin Wah Chay, managing director of BASF Taiwan, adding that “the carbon cycle is not a new concept for BASF.”
In 2007 BASF set about calculating the carbon footprint of its more than 45,000 products. This year, upon certification by a third party, the carbon footprint of every BASF product will be publicly disclosed and made available for customers to freely look up. “Colleagues in the materials department are all screaming, ‘Why aren’t those numbers ready yet?’ Because they are anxious to stress to customers that their products’ carbon footprints are lower,” Chay relates with a chuckle.
‘Transitional products’ account for 30 percent of revenues
BASF has released over 10,000 types of “transitional” innovative products, not only with markedly low carbon emissions, but whose sales are outstripping the market, like biodegradable agricultural film, thinner and more heat-retaining insulation materials, or synthetic leather that does not require the use of organic solvents.
Products like these that satisfy customers’ demands for sustainable development have become the mainstay of BASF’s sales. Reaching sales of 24.1 billion euros last year, accounting for over 30 percent of corporate revenue and reaching company targets three years early, demonstrates the high global demand for transitional products.
BASF conducts life cycle assessments of all of its products, eliminating any product that does not meet sustainability requirements.
Covestro: Plastic made from used oil is getting popular
In early March, Covestro announced that it had reduced its greenhouse gas emissions from 2005 to 2021 by 54 percent, achieving its goal four years earlier than planned. Covestro looks to reach net-zero emissions in energy and production by 2035, even sooner than BASF. This is a far stricter target than many others in the industry.
“How to realize the Paris Climate Treaty targets is a common issue across industry,” relates Wei Guo Lu, Asia Pacific vice president for sustainability and public affairs at Covestro.
Lu relates that Covestro believes that the only way to support our current way of life is to get off of petroleum-based materials and satisfy more customers’ demands for low-carbon products. Covestro has set targets for the ratio of alternative materials to its two leading products, namely TPU and PC.
(Source: Pei-Yin Hsieh)
By 2030, Covestro’s TPU department wants 20 percent of its revenue to come from products not derived from petroleum. These materials could be factory scraps, vegetable starch, restaurant cooking oil, or even CO2.
“The TPU with the world’s highest proportion of biobased materials comes from Covestro’s Changhua plant,” says Wilson Chan, head of APAC TPU business development. At first, Covestro put vegetable starch into TPU, achieving a biobase proportion of 50 percent; for the second generation it used agricultural waste, discarded cooking oil, and turned waste cooking oil into raw material with a biobase ratio of 80 percent. When it first introduced it in 2012, the market was not very responsive, but now the demand has heated up considerably.
Used in smartphone cases, automobile light covers, and medical instruments, PC is found nearly everywhere. And the company has set a target of 80 percent annual growth in PC cyclical materials by 2025.
Covestro is an inventor of polycarbonate, as well as one of the world’s top suppliers. Over the past two years, Covestro has begun partnering with leading Finnish biodiesel firm Neste and Mitsui Chemicals of Japan to use biomaterials made from waste materials to produce PC.
“These days, customers only have one question: What material has the highest proportion of recycled content?” says Roy Cheung, global head of sustainability solutions for Covestro’s polycarbonates business unit, observing the increasing importance of PCR (post-consumer recycling).
Have you read?
♦ Chang Chun turns CO2 into Chemicals
♦ Moving towards a world without oil, how can Taiwan’s petrochemical industry adapt?
♦ How Taiwan’s greenhouse leader found customers in 30 countries
Translated by
David Toman
Uploaded by Ian Huang